Industrial
Simpact/GCE Editorial
June edition of the Gasworld Magazine. The Asset Management Edition
Lorem ipsum dolor sit amet, consectetur adipiscing elit, sed do eiusmod tempor incididunt ut labore et dolore magna aliqua. Ut enim ad minim.
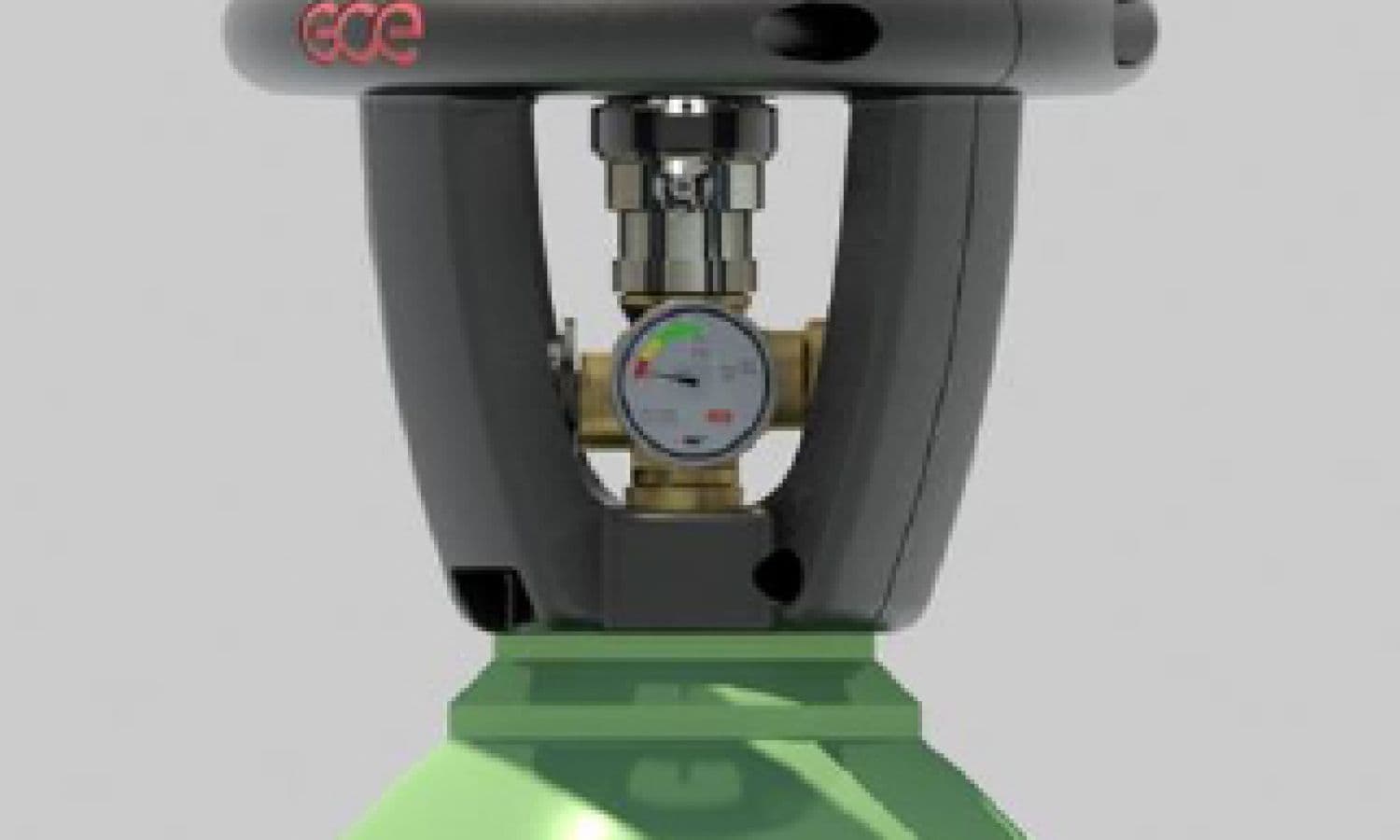
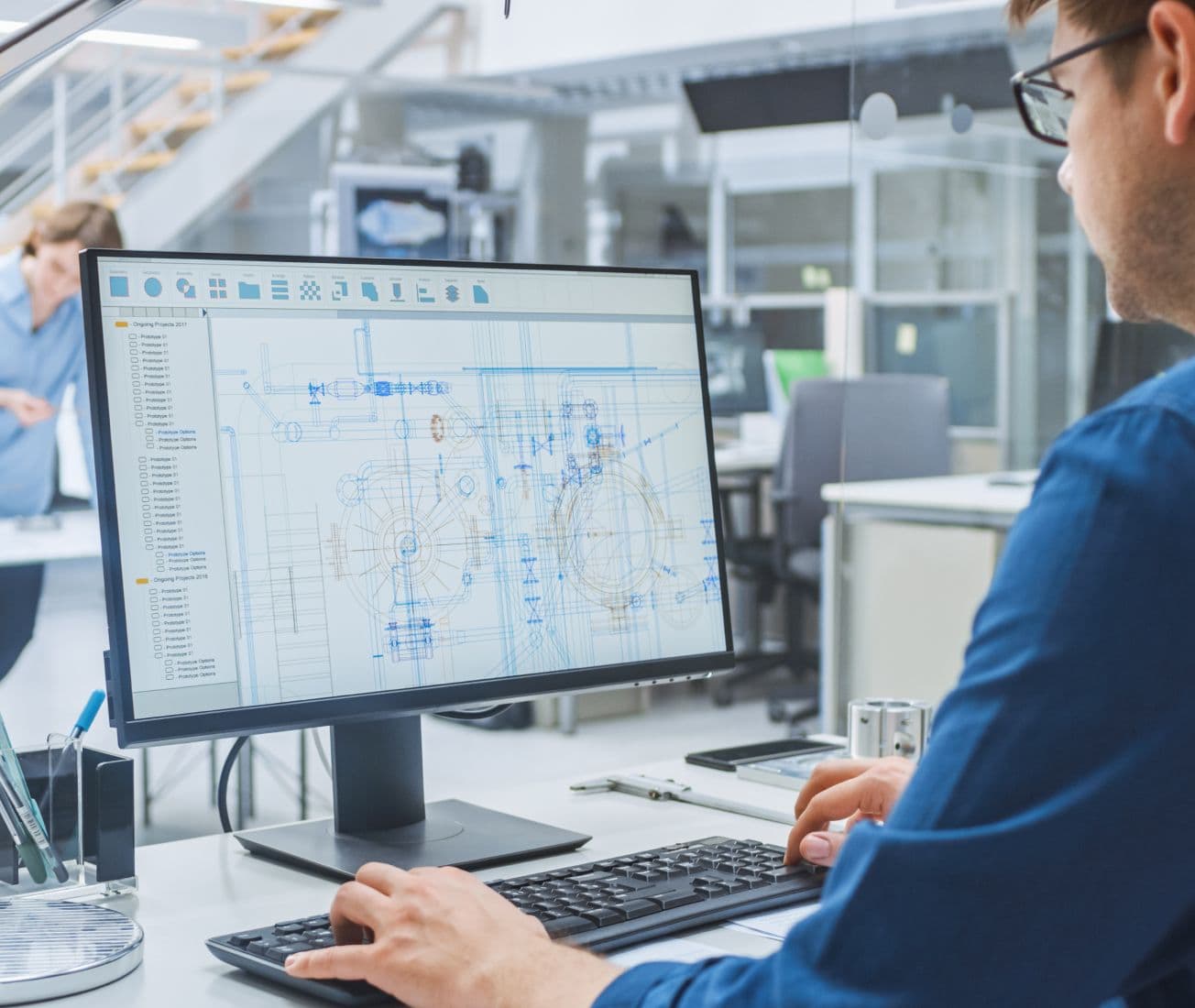
An Introduction to SMART Product Development in the Packaged Gas Industry
A cylinder guard must provide the safe protection of the cylinder valve against impact. However it has other important features which are often overlooked such as ergonomics, for the grip and handling of the bottle, and aesthetics for brand differentiation. Guards come in various designs to suit their applications. Material choices vary with polymers an increasingly popular choice as it enables good value for money and lots of aesthetic options. Other qualities such as corrosion resistance and impact recovery make it a desirable option. However, tools required for the injection moulding are expensive and have long lead times. Getting a design wrong can have a disastrous effect on a company’s product release schedule and bottom line.
Simpact
Simpact Engineering Ltd, based in Warwick, are a CAE (Computer Aided Engineering ) consultancy who specialise in the use of advanced modelling &simulation tools for the virtual development of new products. Originally operating in the automotive market for vehicle crash testing, they have diversified into several markets and been at the forefront of the use of CAE in the packaged gas industry. This article summarises the application of CAE for the advanced design and development of a new protective guard for GCE’s Combilite valve for larger 30L cylinders which needed to pass drop tests at weights of 80kg (EN ISO 1117).
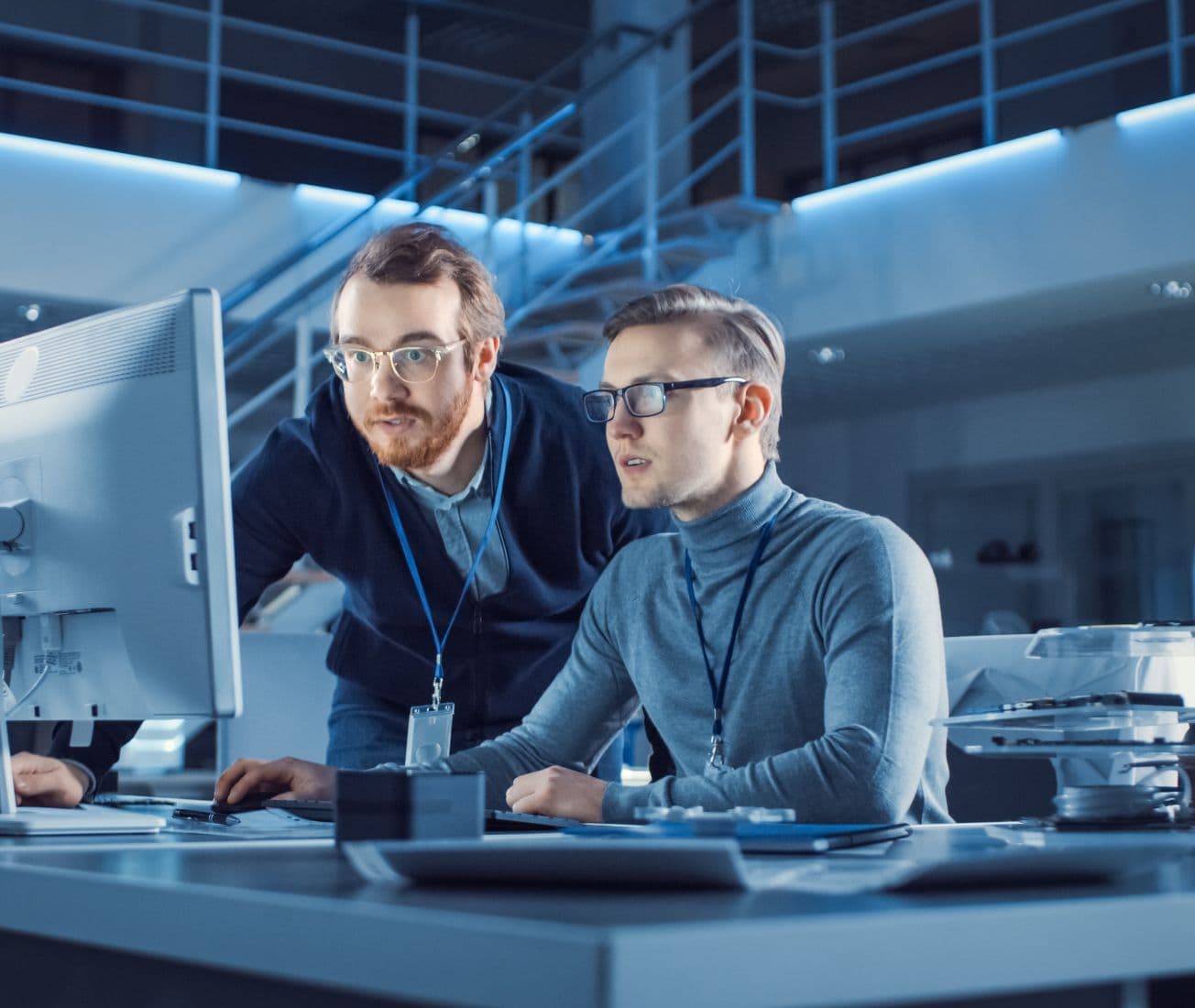
- 1
Concept Design
Step 1, Concept Design – A selection of guard concepts were generated in CAD with the given design brief and initial meetings with GCE. These were generated using CAD design software and used to discuss design space, refill and operating access, ergonomic, material and cost requirements. GCE reviewed these with potential customers and users choosing the highlighted guard for development.
- 2
Finite Element Analysis
An FEA (Finite Element Analysis) model of the complete cylinder assembly with the above guard was generated using the Altair HyperWorks software. This replicated the drop test described in EN ISO 1117. The image below (left) is a cross section of the FEA model in which Simpact have perfected a technique to include the fluid that sloshes inside the cylinder on impact (seen as spheres). The model takes around 2hrs to run on a multi CPU high end PC.
The developed model allowed Simpact to make a detailed assessment (see image below right) of the protection offered to the valve, enabling the geometry of the guard to be tuned to give a robust pass of the drop test. In addition to the drop tests described in EN ISO 1117, GCE had a number of in-house loadcases which were derived from some common handling scenarios. The design was assessed with the FEA model against these and included a crane lift and kerb drop.
Nylon 66 was the chosen material for the guard and as there are different grades and manufactures of this material (such as DuPont Zytel, Grilon etc.) the model was used to investigate which material offered the most economical solution (the FEA model requires material mechanical properties as input and these were obtained from the tensile testing of dog bone samples provided by the materials provider).
- 3
Photorealistic renderings
The CAD model of the guard was updated with the design refinements from Step 2 and rendered using the 3D Studio Max Design software. By building various environments (industrial and medical) this allowed GCE to visualise the new guard in anticipated uses. This proved to be a highly effective way of communicating the new design throughout the company and to potential customers.
- 4
Rapid Prototyping
Once the design was signed off, Simpact’s supplier, Malcolm Nicholls Ltd, was commissioned to produce a rapid prototype model of the guard.
This was printed in a rigid resin using SLA (Stereolithography) technology and the main purpose of the rapid prototype was to allow GCE to carry out a fit and function assessment with their existing valves and cylinders and receive customer feedback.
- 5
Certification & Production
Following certification tests, covering a wider band of temperatures and payload than ISO standards require, the guard will go on sale next month as part of GCE’s product release for an industrial pre-set flow combination valve offering.
The Right First Time Approach applied to this development project gave GCE a competitive edge in bringing a new product to market. The guard passed certification testing first time and is proving to be a great success
Gareth Pemberton
Head of Innovation at GCE
Get in touch
Lorem ipsum dolor sit amet, consectetur adipiscing elit, sed do eiusmod tempor incididunt ut labore et dolore magna aliqua.